An Introduction to Industrial Seals Used in Power Generation Equipment
Aug 13, 2017 Industrial seals | Oil Seals | Material
Seals refer to any adhesive device or material, which joins any two systems together and prevent leakage of fluid under the influence of pressure. These seals are developed using a different process, and are built in adherence with the industrial standards to provide effective performance in various power generation equipment, such as actuators, linear motion devices, gear boxes, etc. Their design, constructions and materials used vary according to the industrial usage. Read this post to get an insight on different types of industrial seals available, the materials used for their construction, and their significance.
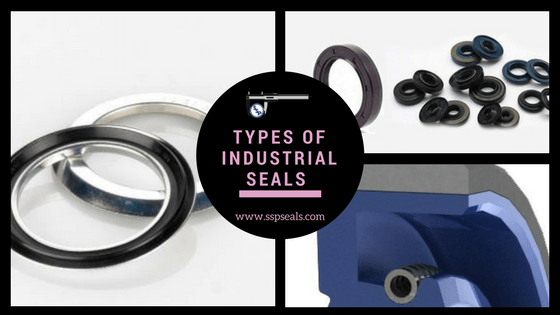
Types of Industrial Seals Used in Power Generation Equipment
Power generation equipment deploys various types of industrial seals, such as bearing seals, grease seals, oil seals, rotary seals and many others. Some preferred industrial seals are explained below:
- Oil Seals: Rubber oil seals prevent the leakage and entrance of any kinds of fluids and dirt. These seals possess an automotive radial lip seal, which creates a thin layer of oil between the shaft and the sealing lip. This thin layer prevents leakage of oil past the sealing lip. Various types of materials are used in the fabrication of oil seals on the basis of external factors like environment pressure, temperature, and shaft size. These materials include Nitrile Buna Rubber (NBR), Polyetrafluorethylene (PTFE), Silicones, and many others.
- Rotary Seals: Rotary shaft seals help prevent entry of mud and water in various components that have oscillating and rotating parts. A rotary seal comes with a sealing lip, a metal case, and a garter spring. Sealing action is provided by elastomeric sealing lip. These rotary seals offers excellent wear resistance, elasticity and low friction properties. These seals are designed and constructed using materials such as Ethylene-propylene Rubber (EPDM), steel, brass and many others.
- Gamma Seals: Gamma seals are designed to eliminate any kind of contamination, moisture and grease. They are widely used in mobile hydraulics and power transmission applications, owing to their heavy duty HDPE construction and leak-proof airtight seal.
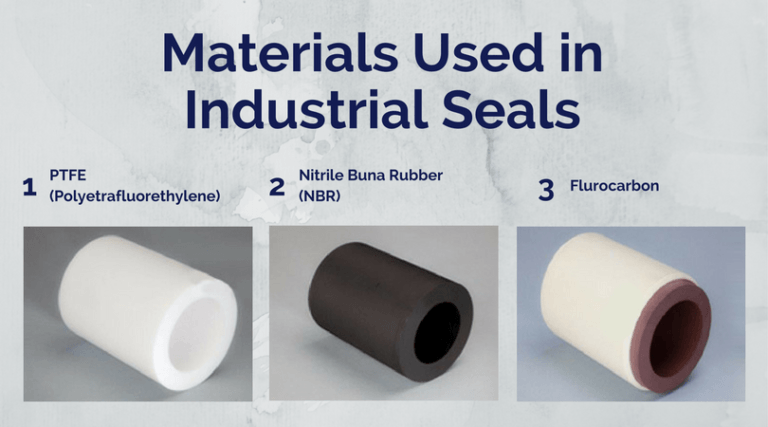
Materials Used in Industrial Seals for Power Generation Equipment
A diverse variety of materials are used in the fabrication of seals. Their specific properties like ability to withstand extreme temperature, corrosion resistance and many others, make them the most widely used material in power generation equipment.
- PTFE (Polyetrafluorethylene): These materials are ideal for applications where low temperature flexibility is required. They are mounded with bronze flashes, carbon, graphite and many other fillers in order to retain their toughness and flexibility. PTFE material is animal-derived, ingredient free compound.
- Nitrile Buna Rubber (NBR): NBR is a member of butadiene and unsaturated synthetic rubber copolymers of acrylonitrile (ACN). They have high acrylonitrile content, and offer better resistance to ageing, flame, petrol, and ozone.
- Flurocarbon: Flurocarbon are used for lip seals, wipers and many other specific seals. They offer high resistance to heat, ozone and various other chemicals. Flurocarbons are highly resistant to ultraviolet light and ozone, hence they are widely used with alcohol and aromatic fuels.
Choosing the right kind of industrial seals can help you improve the quality, performance, and durability of the power generation equipment. If you are looking forward to buy any kind of industrial seal for your power generation equipment, you can bank on SSP Manufacturing, Inc. The company is one of the leading providers of standard and custom industrial seals in the USA.
Related Post