How to Solve Some Common Sealing Problems?
Sep 24, 2024 Industrial seals
Sealing is an integral part of many industrial processes, and in fact, airtight seals are required across applications from food, chemicals, and pharmaceuticals to oil & gas, engineering, and more. This includes sealing final products as well as using O-rings and gaskets to prevent pressure and leakage issues in different equipment used across industries. However, sometimes industrial sealing solutions may be faulty, causing leakages in terms of pressure, heat, moisture, and so on. Poor sealing solutions can cause contamination and bring down process efficiency. Thankfully, you can easily fix these common sealing failures. This post discusses how to fix sealing problems effectively and reduce risk and damage.
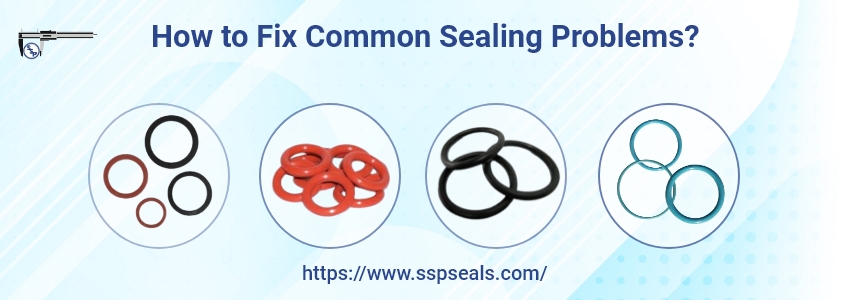
Common Sealing Failures and Their Solutions
The filling and capping machines have been used in hand sanitizer production for several decades; however, demand hugely surged during the COVID-19 pandemic. Even now, the demand is pretty high, although not as much as it was during the pandemic. Let’s understand why these machines play a crucial role in this process.
Here are some common causes of sealing failures and damage.
- Incorrect installation:Wrongly installed or aligned seals may cause friction and subsequent wear. At times, the seal may also turn inside out when installed, leading to leakage and contamination.
Solution: To avoid friction, the seal lip must be well-lubricated. The geometry of the seal must be adjusted based on its material, such as PTFE or polypropylene. Visually inspecting the installation and refitting after each use is also important.
- Heat checking: In some seals containing metals and ceramics, cracks may appear from the center of the ring. This is called heat checking, which may happen due to low specific gravity at high speeds and pressures and inadequate lubrication. This may also produce a sound during operation.
Solution: To avoid this situation, one needs to ensure enough seal lubrication and coolant flow at the face of the seal in case your process generates heat.
- Coking and grooving of O-rings and gaskets:Coking leaves a coal-like black buildup on the side of the ring exposed to the outside atmosphere. This may happen if your seal material becomes easily oxidized or due to contamination.
Solution: If this is due to contamination, you can remove the sludge and debris with steam, and flush the seal. Also, consider oxidation-resistant face materials for your seal.
- Corrosion:If your seal is exposed to harsh chemicals, acids, and more continually, it may suffer a chemical attack that causes pitting and corrosion of the seal.
Solution: You must select the right material for your seal, which can endure constant chemical exposure.
- Excessive pressure:Excess pressure buildup in the seal housing can damage it.
Solution: It is essential to maintain adequate pressure. The seal housing must neither be over nor under pressurized.
- Lack of maintenance:Physical inspection and maintenance are essential for any equipment. If not cleaned after each use, the seal may be contaminated and cause debris buildup.
Solution: Basic cleaning and maintenance are a must to avoid seal failure. For maintenance tips, refer to the manufacturer’s guidelines for maintenance tips.
- Issues in rotating shaft:Shaft dynamics play a crucial role in rotating equipment and its seal function. Any issues with the rotational movement of these blades impact the seal. In case of issues in bearing, the alignment of the shaft changes, and the seal may undergo compression.
Solution: The design and alignment of the shaft and bearing must be rectified, and the alignment of the entire equipment must be checked.
- Blistering:This causes small circular sections on the seal, which may lead to leakage. This is a sort of thermal attack on the seal, which may happen due to improper cooling after the process. In case, your application deals with viscous fluids, the oil within them may be forced out towards the seal face, resulting in blistering.
Solution: Reduce the number of start and stop functions of your equipment with mechanical seals, especially in case of exposure to viscous fluids. Also, consider a non-porous seal face material to prevent the effects of blistering.
- Environmental parameters:Air and water are essential parameters that must be kept in check. Excess air may cause bubbles around the seal. Also, high humidity or moisture in the area around the equipment or system may build up moisture and increase the water content in the fluid to be pumped.
Solution: It is important to measure moisture content in the area as well as maintain oil levels to avoid seal damage.
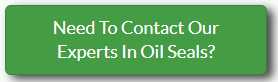
Are you looking for the right solutions for your O-ring seal problems or do you need to replace the seals in your application? If yes, ensure you partner with reliable manufacturers and suppliers that offer high-quality gasket sealing solutions and other types of seals as per your requirements. If you are looking for food or pharmaceutical applications, ensure the industrial oil seals are FDA- approved. SSP Manufacturing Inc. has a market presence of more than three decades and offers premium quality custom seals for several industrial applications. Contact their team today at 1-908-852-3125 or via email at gm@sspseals.com Or +1 908-852-3125.