Comparing Rubber vs. Silicone Seals: Which is Best for Your Project?
Oct 22, 2024
Seals and gaskets are essential components in various industrial settings that ensure the integrity and efficiency of machinery by preventing leaks and contamination. Their major role includes maintaining pressure, containing fluids, and protecting against external environmental factors. These seals and gaskets are made from different materials, including rubber and silicone. These rubber and silicone seals are prominently used in modern applications due to their versatile properties and adaptability to different conditions. This post delves into a detailed comparison between rubber and silicone seals, highlighting their unique attributes and performance characteristics.
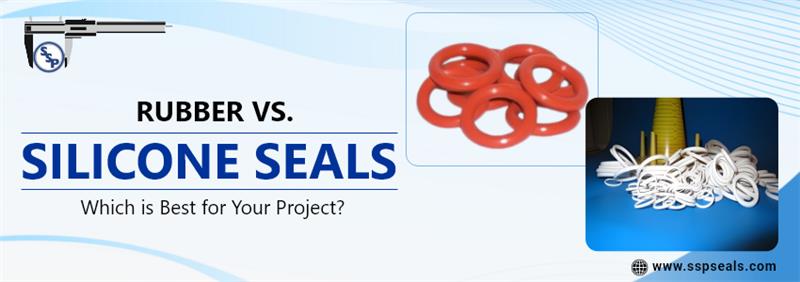
Comparing Rubber and Silicone Seals for Industrial Applications
In industrial applications, the choice of seal material is critical to ensuring optimal performance and longevity of equipment. Rubber and silicone are two of the most commonly used materials for seals, each offering unique advantages. Understanding these differences can help you select the right seal for your specific needs.
Here are some common causes of sealing failures and damage.
- Rubber Seals: Rubber seals are known for their exceptional flexibility, resilience, and durability. They are made from synthetic rubbers, such as nitrile, styrene butadiene, fluorocarbon rubber, ethylene propylene rubber, neoprene and so on. Rubber seals are commonly used in industries such as automotive, aerospace, and plumbing due to their ability to maintain a tight seal under varying pressures and temperatures. The key characteristics of rubber seals include:
- Flexibility: Rubber seals, including Fluorocarbon Rubber (FKM) and Ethylene Propylene Rubber (EPDM), can withstand significant deformation without losing their sealing capabilities, making them ideal for applications involving dynamic or moving parts. This flexibility allows rubber seals to adapt to surfaces and maintain their integrity under various mechanical stresses.
- Durability: These seals resist wear and tear, providing long-lasting performance even in harsh environments. Rubber’s inherent toughness helps it endure repeated use and exposure to abrasive materials, extending the lifespan of the seal and reducing maintenance costs. FDA White Buna is an example of a durable rubber seal used in food and beverage applications.
- Chemical Resistance: While rubber seals offer good resistance to many chemicals, including Fluorocarbon Rubber (FKM), they may degrade when exposed to certain oils, solvents, and fuels. This limits their use in environments where they come into contact with aggressive substances that can cause swelling or brittleness.
- Cost-Effective: Rubber, including Ethylene Propylene Rubber (EPDM) and FDA White Buna, is generally less expensive than silicone, making it a cost-effective choice for many applications. Its lower cost does not compromise its performance, making it an attractive option for large-scale industrial use where budget constraints are significant.
- Temperature Resistance:Custom rubber seals, such as nitrile rubber seals, can typically withstand temperatures ranging from -30°C to 120°C. This makes them suitable for various applications, although they may not be ideal for extreme temperature conditions. Maintaining performance within this temperature range is crucial for many industrial processes. Fluorocarbon Rubber (FKM) is known for its superior temperature resistance, making it suitable for more demanding environments.
- Silicone Seals: Silicone seals are favored for their superior temperature resistance and excellent chemical stability. They are widely used in the medical, food processing, and electronics industries where purity and performance at high temperatures are critical. The key characteristics of silicone seals include.
- Temperature Resistance: Silicone can withstand extreme temperatures, ranging from -60°C to 200°C, without losing its properties, making it suitable for high-temperature applications such as engine compartments, oven doors, and other environments where thermal stability is essential.
- Chemical Stability: Silicone seals, including Vinyl Methyl Silicone Rubber (MVQ Silicone), exhibit excellent resistance to a wide range of chemicals, including acids, bases, and solvents. This chemical inertness makes them ideal for use in chemically aggressive environments, ensuring that the seals do not react with or degrade in the presence of various substances.
- Flexibility and Elasticity: While not as flexible as rubber, silicone still offers good elasticity, maintaining its shape and seal integrity over time. Silicone’s ability to rebound and maintain its form under stress is crucial for applications that require consistent sealing performance over extended periods.
- Biocompatibility: Silicone is non-toxic and hypoallergenic, making it the material of choice for medical and food-grade applications. Its biocompatibility ensures that it does not cause adverse reactions when in contact with biological tissues or food products, making it suitable for medical devices, implants, and food processing equipment.
- Cost-effective: While silicone seals can be more expensive than rubber seals, they are cost-effective in the long run due to their durability and lower maintenance requirements. The longevity and high performance of silicone in demanding environments can lead to reduced downtime and replacement costs, offering better value over time.
Both rubber and silicone seals offer unique advantages for industrial applications. Rubber seals are flexible, durable, and cost-effective, making them ideal for dynamic and high-wear environments. They provide long-lasting performance under mechanical stress and are budget-friendly. Silicone seals provide superior temperature resistance and excellent chemical stability, making them perfect for high-temperature and chemically aggressive settings. Their biocompatibility makes them suitable for medical and food-grade applications, ensuring safety and reliability in sensitive environments.
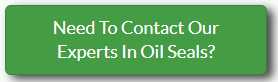
If you are searching for a reliable silicone O ring suppliers for your industrial applications, SSP Seals offers a wide range of rubber and silicone seals tailored to meet your specific requirements. They provide high-quality custom rubber seals, including NBR rubber seals, PTFE seals, FKM seals, EPDM, and PEEK, as well as molded gaskets, rubber parts and silicone O-rings for diverse environments. For any queries or requirements for your next project, contact their sales team today via email at gm@sspseals.com Or +1 908-852-3125.
Related Post