Sealing Technology for Critical Applications: A Comprehensive Guide
Jun 28, 2024 Industrial seals
Seals and gaskets are vital to ensure airtight sealing and operational safety and applicable across industries such as automotive, aerospace, and oil and gas. These are specially designed seals suitable for harsh industrial environments and temperature as well as pressure ranges. The use of advanced materials such as fluoropolymers and thermoplastic elastomers in making these seals enhances their resistance to harsh environments. With precision engineering and additive manufacturing, customization and optimized configurations can be achieved. Technological advancements have driven their evolution, thus improving the reliability, efficacy, and safety in manufacturing processes. Smart seals equipped with sensors enable real-time monitoring for predictive maintenance, while sustainable solutions address environmental concerns. This post discusses the technological and other innovations in sealing technology.
Current Trends in Sealing Technologies
According to a report, the global industrial seals and gasket market was valued at USD 26,662.62 million in 2022. It is projected to reach USD 36,430.27 million by 2028, growing at a CAGR of 5.34%. This growth is attributed to advanced technologies and the widespread use of these products across diverse industries. From hydraulic systems in aviation to medical seals in healthcare and engine seals in automobiles, sealants play a critical role in various industrial products and operations. Research and innovation are giving rise to novel sealing technologies rapidly entering the market. This may help meet the evolving demands of multiple sectors. Here are some recent developments in sealing technology that may create a huge difference in the market.
- Advanced PTFE Radial Shaft Seals:The development of rotary lip seals, utilizing Teflon-like polytetrafluoroethylene (PTFE), marks an important stride in sealing technology. PTFE’s fluorocarbon composition provides a low co-efficient of friction and distinct nonstick properties, along with resistance to temperature variations, electrical effects, and corrosive reactions. It is perfect for sealing rotating shafts and bores. These seals feature an inner lip for shaft attachment and an outer metal shell for a snug fit into the bore, supplemented by a gasket to avoid leaks. Leveraging PTFE’s low friction nature, these seals make high surface speeds, augmenting efficacy and reliability in different industrial applications.
- Enhancing Production Efficiency through 3D Printing: The development of sealants, specifically O-ring sealants, marks a substantial progress in sealing technology. Traditionally, methods such as compression and injection molding have been employed to shape these sealants by implementing heat and pressure to the material in a mold, resulting in notable waste and high expenses. 3-D dimensional printing builds objects by adding material layers by layers from a digital blueprint, improving the speed of prototyping and production, decreasing costs, and reducing waste. Large companies in this segment stock over 8,000 O-ring sizes, designed from specialized rubbers such as Viton, nitrile, and fluorosilicone, suitable for uses ranging from medical seals to aircraft engines.
- FFKM Sealants for boosted durability: The advancement of FFKM sealants signifies an important development in the sealing segment, offering exceptional resistance to extreme temperatures and chemical conditions. FFKM has higher fluorine and lower hydrogen content than other fluoroelastomers. It combines the chemical resilience of Teflon with the durability of elastomers, enduring temperatures up to 600 degrees Fahrenheit, resisting corrosive chemicals that would degrade most materials. It has the ability to withstand continuous load strains, which makes it perfect for aerospace applications. It is now used as a sealant in gearboxes and bearing chambers in this sector. These innovations are paving the way for future developments in sealing technology.
FFKM O-rings
Technological Advancements in Seals and Gaskets
Technological advancements in seals and gaskets are revolutionizing the industry. Here are some relevant pointers.
- Nanotechnology boosts sealing efficiency and durability through advanced material integration.
- Digitalization and IoT tools enable predictive maintenance by monitoring performance in real-time.
- Industry 4.0's automation and analytics streamline production, ensuring consistent quality.
- Smart sealing solutions with embedded sensors adjust performance autonomously, reducing downtime.
- Adoption of green technologies promotes eco-friendly materials and processes, maintaining high performance standards.
- These innovations collectively assist industrial seal manufacturers in advancing towards enhanced reliability, efficiency, and sustainability across various applications.
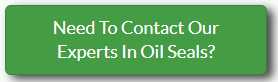
If you’re looking for top-quality seals and gaskets that offers exceptional reliability, efficiency and sustainability, look no further than SSP seals, an experienced and known industrial seals manufacturer. Explore their offerings to discover a wide range of cutting-edge sealing solutions designed to meet your diverse industrial needs. For any inquiries, feel free to reach their team via phone or email.
Related Post