An Overview of Dynamic Sealing
Jul 13, 2016 Industrial seals | Oil Seals
Dynamic seals are the type of seals used to produce a barrier between stationary or moving surfaces in linear, oscillating, and rotary motion applications.
These seals are used to separate or retain fluids, pressure, and remove contaminants. This post introduces a reader to various types of dynamic seals used in applications, and criteria for selection.
Categorization of Dynamic Seals
Dynamic seals are classified into the following two categories:
- Clearance Seals: These positive clearance seals help inhibit contact between the mating surfaces.
- Contact Seals: These seals create sealed interface by applying pressure to the surface.
Understanding the Various Types of Dynamic Seals
The following are some of the popular types of dynamic seals used across process industries.
- Hydraulic and Pneumatic Seals: These seals are used in reciprocating, oscillatory, and rotary motion devices. These seals are employed in high pressure applications to restrict fluid flow, and avoid foreign particle entry. Hydraulic seals are used in hydraulic devices, where they convert fluid power into a linear motion. However, pneumatic seals are used in gaseous, or air mediums. This may include rod seals, piston seals, flanges, and U-cups.
- Oil and Grease Seals: These seals feature flexible lip that cover the housing or shaft to prevent the leakage of fluid. Some of these seals feature spring that help maintain contact between the lip and shaft. These seals are used to prevent the lubricant leakage, and intrusion of harmful contaminants. These seals are now becoming an integral part of various industrial machines and automobiles.
- Exclusion Seals: These seals include scrapers and wipers that support the reciprocating or sliding motion. These seals help scrubbing retracting rod off dust, ice, or other particles. The wipers need regular inspections to ensure proper working.
- X-Rings: These seals are also known as quad rings, and are used for long stroke applications. This seal is distinguished by its cross-section, which is shaped like a four-leaf clover. This seal is ideal for applications where wider seals are required.
- Clearance Seals: These are positive clearance seals, which have no contact with the housing or shaft. These seals are used to restrict passage of liquids, solids, and gaseous contaminants into the device. Many of these seals contain a stator and a rotor, and are used for extreme temperature operations.
- Piston Rings: These are made from metals, and are used to seal cylinders. These seals can resist high temperature, and are available in a wide variety of configurations. Some of the popular types of piston rings include split rings, compression rings, and cord rings.
- O-Rings: These are one of the most popular types of dynamic seals in use. O Rings are designed to be bi-directional, and are easy to install.
- Isolator Seals for Bearing: These seals protect bearings from leaking lubricants, and help avoid contaminants from entering into the bearing.
- Lip Seal: These seals are available in many variations. The seal is alternately known as a lipped seal, and it offers sealing in one direction. These seals provide stability in dry, reciprocating, or long stroke applications. These seals are regularly used in high pressure applications.
Materials Used for Construction
Dynamic seals are made from either of these materials:
- Metals: Metallic materials such as stainless steel, cast iron, and bronze are first choice for making dynamic seals. The sintered bronze is ideal for low lubrication applications, but not for heavy loaded applications. Cast iron seals feature traces of carbon and steel. Stainless steel seals are corrosion and chemical resistant, and are used for high pressure applications.
- Polymer or Rubber: The dynamic seals made from elastomers, polymers, rubbers, and a variety of special materials. Made from EPDM (Ethylene Propylene Diene Monomer), the seals are used in various industrial applications. Some of the commonly used rubbers or polymers include polyacrylate, fluoroelastomer, nitrile, fluorosilicone, polyamide, polyoxymethylene, polyetheretherketone, urethane, polyurethane, and polytetrafluoroethylene
Criteria for the Selection of Dynamic Seals
The selection of dynamic seals is made on the basis of the following considerations:
- Type of Application
- Environmental Serviceability
- Ease of Installation
- Reliability and Operational Performance under Extremes
- Resistance to Extrusion between Mating Parts
- Tolerance to the Sealing Medium
- Sealing Orientation
- Dimensions
- Materials used for Construction
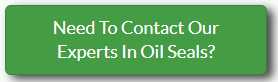
The seal life depends on the factors such as material selection, the presence of appropriate lubrication, and surface finish of the seal.
With so many varieties of dynamic seals for consideration, there are all chances of confusion. You can always approach the manufacturer, or an industry expert to make the right selection. If you are doing it by yourself, take care to keep the previously mentioned selection criteria in mind.
Related Post