Innovative Sealing Solutions for High-Pressure Environments in Oil and Gas Applications
Mar 28, 2025 Industrial seals | Oil Seals
In high-pressure environments across oil and gas applications, reliable sealing solutions are not just an engineering preference; they are an operational necessity. From deep-sea exploration to high-temperature processing units, components are subjected to extreme pressure, fluctuating temperatures, and aggressive chemicals. Inadequate or failed sealing can lead to catastrophic consequences such as equipment breakdown, environmental contamination, production downtime, and even loss of life. This makes understanding and deploying effective sealing technologies crucial for maintaining safety, operational efficiency, and regulatory compliance. High-performance seals act as critical safeguards, especially in upstream and downstream processes, ensuring the integrity of equipment under the most demanding conditions. This post delves into key features of innovative sealing solutions, types of seals for the oil and gas industry, benefits of using advanced sealing technologies in oil and gas, and future trends in high-pressure sealing solutions.
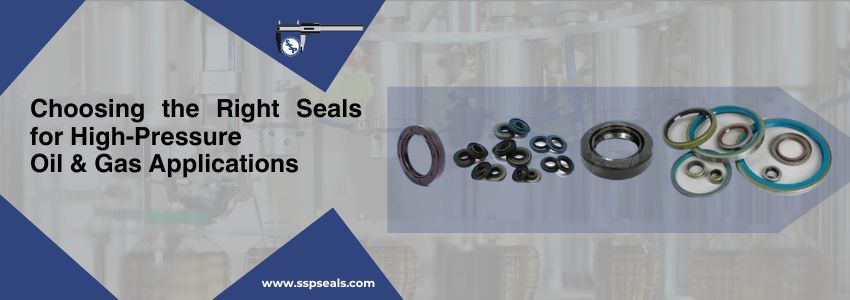
Key Features of Innovative Sealing Solutions
Sealing systems designed for oil and gas applications must meet stringent demands to perform reliably under high pressures and temperatures. Innovative sealing technologies incorporate advanced materials and design features to improve longevity, performance, and adaptability. These features ensure resistance to aggressive media, withstand extreme mechanical loads, and offer superior sealing efficiency.
- High Chemical Compatibility: Seals must endure exposure to corrosive chemicals, sour gases, and hydrocarbon media. Modern seal materials offer resistance to hydrogen sulfide, methane, and CO₂, preserving seal integrity even in harsh conditions.
- Thermal Resistance: High-temperature seal materials like PTFE and its derivatives exhibit excellent PTFE thermal conductivity, maintaining structural stability and sealing performance across a wide thermal range.
- Pressure Tolerance: Advanced sealing technologies can handle pressure ratings exceeding 20,000 psi. Seals are engineered to prevent extrusion and maintain shape under fluctuating pressure conditions.
- Low Compression Set: Innovative elastomers and thermoplastics used in seals exhibit low compression set, allowing the seal to maintain tight contact with mating surfaces for extended periods.
- Custom Design & Modularity: Newer sealing solutions are highly customizable to accommodate different geometries, environmental exposures, and dynamic conditions like axial and radial motion.
- Abrasion and Wear Resistance: Innovative compounds used in oil and gas drilling sealant compounds ensure extended service life, minimizing the frequency of maintenance shutdowns.
- Rapid Gas Decompression (RGD) Resistance: Seals with built-in RGD resistance prevent blistering or rupturing when transitioning from high to low pressure quickly, a frequent scenario in drilling applications.
Types of Seals for the Oil and Gas Industry
Given the wide range of applications within oil and gas—from upstream drilling to downstream refining, different types of seals are deployed depending on the mechanical and environmental challenges they face. The choice of sealant solutions for oil and gas drilling is influenced by pressure, temperature, media, and motion.
- O-Rings: Used extensively in static and low-dynamic applications, O-rings offer a simple yet highly effective sealing method. Made from materials such as FKM, NBR, and PTFE, they provide reliable sealing under moderate pressures and temperatures.
- T-Seals: T-seals combine the advantages of O-rings and back-up rings, offering enhanced stability in high-pressure environments. These are ideal for reciprocating applications where extrusion is a concern.
- Spring-Energized Seals: Designed for extreme pressures and wide temperature fluctuations, these seals utilize a metal spring to maintain contact between sealing surfaces. These are perfect for cryogenic and high-heat systems.
- V-Packings and Chevron Seals: These stacked sealing components adapt well to fluctuating pressures and are used in pumps, valves, and hydraulic cylinders. The multiple lips provide enhanced sealing performance.
- Metal Seals: Where elastomeric materials may fail, metal seals step in. These seals handle the most aggressive temperatures and pressures and are typically used in pipeline connections and wellheads.
- Bonded Seals (Dowty Seals): Combining metal and elastomer elements, bonded seals offer a secure, leak-proof interface for bolted joints. Their versatility makes them ideal for hydraulic fittings and flange connections.
- Gasket Seals: Often customized for large, flanged joints in high-pressure processing systems, gaskets are made from metal-reinforced composites or high-performance thermoplastics to ensure leak-proof sealing.
Benefits of Using Advanced Sealing Technologies in Oil and Gas
Leveraging advanced oil and gas sealing solutions offers substantial advantages across safety, cost-efficiency, and performance. As the industry continues to operate in deeper wells and more corrosive environments, these innovations become indispensable for risk mitigation and operational optimization.
- Improved Safety and Reliability: Advanced seals minimize the risk of gas leaks, blowouts, and mechanical failure, which can otherwise lead to catastrophic accidents.
- Extended Equipment Life: Innovative materials like engineered PTFE and other fluoropolymers protect critical components from erosion, corrosion, and chemical attack, thus extending equipment longevity.
- Reduced Downtime: Durable sealing systems reduce the frequency of maintenance interventions, resulting in uninterrupted operations and minimized production loss.
- Enhanced Operational Efficiency: Efficient gas sealing solutions contribute to better system pressure retention and reduced energy consumption, translating into increased overall productivity.
- Regulatory Compliance: Oil and gas drilling operations are subject to strict environmental and safety standards. Advanced seals help maintain compliance by preventing leakages and contamination.
Future Trends in High-Pressure Sealing Solutions
Future innovations in oil and gas sealing solutions are likely to focus on adaptability, intelligence, and sustainability.
- Smart Sealing Systems: Integration of sensors and IoT-enabled diagnostics will allow seals to monitor their own wear, temperature exposure, and leakage probability, enabling predictive maintenance.
- Advanced Composite Materials: Development of hybrid materials combining the best of metal and polymer properties will offer superior sealing performance in ultra-high-pressure zones.
- Sustainable Seal Materials: Environmental concerns are driving research into biodegradable or recyclable sealing compounds that still meet the durability and thermal demands of oilfield applications.
- Self-Healing Seals: Emerging research is exploring seals that can self-repair micro-damages or abrasions, thus significantly extending seal life and reducing operational interruptions.
- Improved Rapid Gas Decompression Resistance: Seals are being engineered to provide even higher RGD resistance, especially for use in deep-water and high-flow gas systems where pressure shifts are frequent.
- Customization Through Additive Manufacturing: 3D printing of seals using high-performance materials allows faster prototyping and tailored solutions for non-standard equipment or repair-on-demand scenarios.
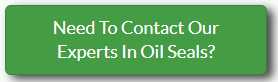
When it comes to reliable, efficient, and sustainable oil and gas sealing solutions, SSP Seals stands out as a trusted name in the industry. As a well-known manufacturer of high-performance seals and gaskets, SSP offers a wide array of advanced products tailored for demanding industrial applications. From high-pressure environments to complex machinery, their solutions ensure lasting performance. Have any queries or requirements? Connect with their expert team via via email at gm@sspseals.com Or +1 908-852-3125.