Industrial gaskets are the most important components used for sealing the gap between two moving objects to make them airtight, liquid-tight or dust-tight. Owing to several benefits of these gaskets, they have become a must-have part of most industrial machinery and equipment. Gaskets are not only used to prevent leakage but also to ensure that there is no damage to the system. Their use is widespread with applications across a wide range of industries including oil, gas, automotive, medical, food processing, marine and refinery operations. To meet the varying demands of industries, gaskets are produced in a wide range of materials, each with their own set of benefits and drawbacks. Hence, to ensure the right selection, it is important to know about the materials with which the gaskets are made. This post is thus aims to list a five such popular materials used for making industrial gaskets.
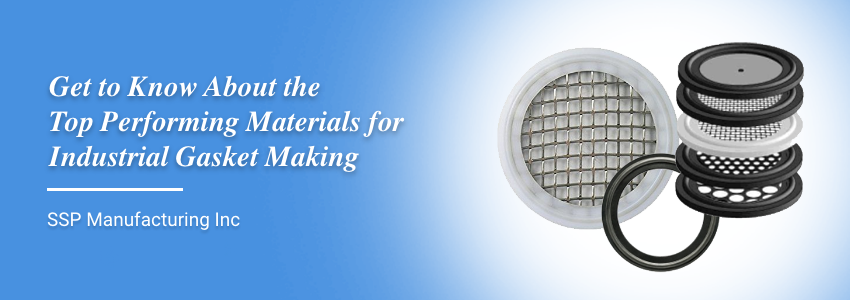
Top Materials Used to Make Industrial Gaskets
Gaskets have been used in commercial and industrial settings since decades. They are commonly used as flexible seals in pipes and pressure vessels, and thus prevent leaks in valves, flanges, and other devices. To meet the requirements of these applications, gaskets are usually made of the finest quality materials. A few of them are:
• Ethylene Propylene Diene Monomer,(EPDM): EPDM rubber material is one of the most popular rubber materials used in gasket making. It is a good alternative to nitrile (Buna N, NBR) and other general-purpose rubbers like SBR, and Viton. EPDM has been found to resist concentrated hydrochloric acid, caustic soda, many organic acids, and aliphatic hydrocarbons. Being an elastomeric material, it can be stretched up to twice its length without any degradation in performance. Gaskets made using EPDM rubber material are used in a wide range of sealing applications including automotive, construction, packaging, and general industrial.
• Nitrile Butadiene Rubber (NBR): NBR material is made from the polymerization of butadiene and acrylonitrile. The NBR material is widely used in the making of industrial gaskets owing to its excellent wear, heat, and chemical resistance. The
NBR is suitable for a wide range of applications, including industrial equipment, fuel tanks, hoses, and chemical processing equipment, among others.
• Polyetrafluorethylene (PTFE): PTFE is a high-temperature, chemically inert plastic that has been used as a gasket material for many years. PTFE stands for polytetrafluorethylene and has a wide range of material properties, including high-temperature strength, and low coefficient of friction. In recent years, PTFE has seen some market share erosion due to its inability to withstand harsh chemicals present in petroleum and petrochemical applications. However, it is still the gasket material of choice in many industries due to its unique combination of properties. PTFE has good thermal stability, and can withstand a wide range of temperatures, and resist most chemical solvents and acids.
• Fluorocarbon Rubber (FKM ): The material is largely used in the making of industrial gaskets owing to its high-temperature resistance, and good chemical stability. It has good creep resistance, improved heat aging property, fine mechanical properties, and excellent ozone resistance. Gaskets made from FKM are widely used for sealing purposes in petroleum, chemical, heating and air-conditioning, power plant and metallurgy industries, among others.
Gasket manufacturing is all about precision. If a gasket manufacturer chooses a low-quality material, it can lead to problems such as leakages, and poor sealing, among others. Hence, it is highly recommended to get the gaskets from those manufacturers like SSP Manufacturing who use the finest quality materials in gasket production. With several years of experience in the industry, the team SSP Manufacturing knows about the several grades of materials that perform under several operating conditions. Get in touch with the team to know more about the gasket materials and their peculiar properties. This would in turn help you choose the right type of gasket that performs the best in your applications.